Professional Suggestions on What is Porosity in Welding and Exactly How to Resolve It
The Science Behind Porosity: A Comprehensive Guide for Welders and Fabricators
Understanding the detailed systems behind porosity in welding is important for welders and makers aiming for flawless workmanship. From the make-up of the base materials to the intricacies of the welding process itself, a wide range of variables conspire to either aggravate or alleviate the existence of porosity.
Recognizing Porosity in Welding
FIRST SENTENCE:
Examination of porosity in welding reveals crucial insights into the integrity and high quality of the weld joint. Porosity, identified by the visibility of cavities or spaces within the weld steel, is a common issue in welding processes. These voids, otherwise properly dealt with, can compromise the architectural integrity and mechanical residential or commercial properties of the weld, leading to potential failings in the ended up item.
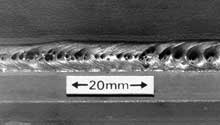
To detect and evaluate porosity, non-destructive testing techniques such as ultrasonic testing or X-ray examination are frequently employed. These methods permit the identification of interior issues without compromising the honesty of the weld. By examining the size, form, and circulation of porosity within a weld, welders can make educated choices to improve their welding processes and achieve sounder weld joints.
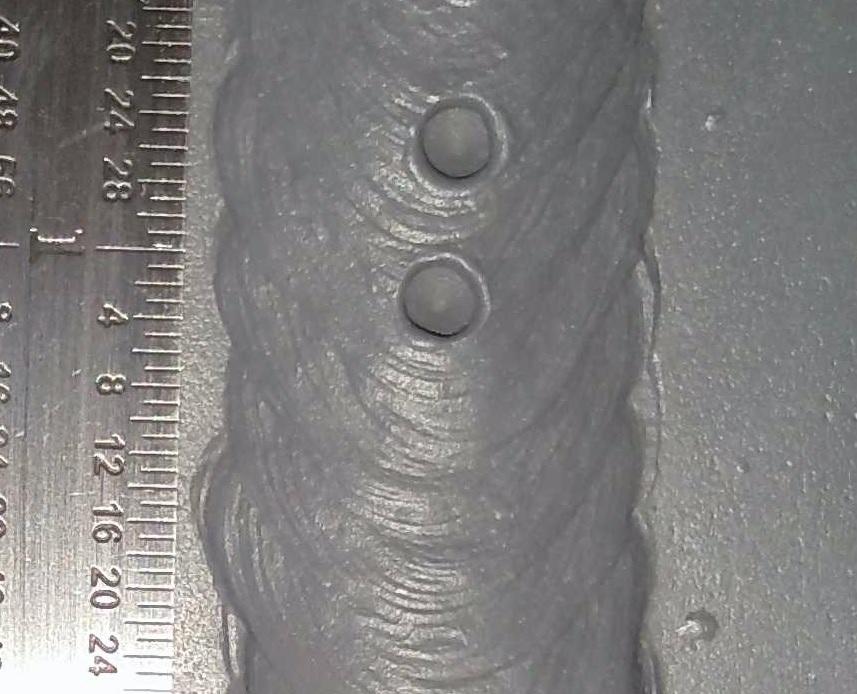
Factors Influencing Porosity Formation
The event of porosity in welding is affected by a myriad of elements, ranging from gas securing performance to the complexities of welding specification setups. One essential variable adding to porosity formation is inadequate gas shielding. When the securing gas, normally argon or CO2, is not successfully covering the weld pool, climatic gases like oxygen and nitrogen can contaminate the liquified steel, causing porosity. Additionally, the tidiness of the base products plays a substantial role. Pollutants such as rust, oil, or wetness can evaporate during welding, creating gas pockets within the weld. Welding criteria, including voltage, current, travel rate, and electrode kind, also effect porosity development. Making use of incorrect settings can produce excessive spatter or heat input, which subsequently can lead to porosity. The welding technique employed, such as gas steel arc welding (GMAW) or protected steel arc welding (SMAW), can affect porosity development due to variations in warm distribution and gas protection. Recognizing and regulating these elements are essential for decreasing porosity in welding operations.
Effects of Porosity on Weld Top Quality
The existence of porosity likewise weakens the weld's resistance to rust, as the entraped air or gases within the voids can respond with the surrounding atmosphere, leading to degradation over time. Additionally, porosity can prevent the weld's capacity to withstand pressure or effect, additional threatening the general high quality and reliability of the bonded framework. In crucial applications such as aerospace, automobile, or structural constructions, where safety and resilience are paramount, the harmful results of porosity on weld quality can have extreme check this site out consequences, stressing the relevance of decreasing porosity via correct welding strategies and treatments.
Strategies to Minimize Porosity
Furthermore, using the suitable welding parameters, such as the proper voltage, existing, and travel speed, is vital in preventing porosity. Preserving a regular arc length and angle during welding additionally helps minimize the likelihood of porosity.

Furthermore, picking the right shielding gas and maintaining appropriate gas circulation rates are important in reducing porosity. Utilizing the ideal welding method, such as back-stepping or employing a weaving motion, can additionally aid disperse warm uniformly and decrease the chances of porosity formation. Lastly, ensuring correct air navigate to these guys flow in the welding atmosphere to get rid of any kind of potential sources of contamination is important for attaining porosity-free welds. By executing these strategies, welders can successfully reduce porosity and create high-quality bonded joints.
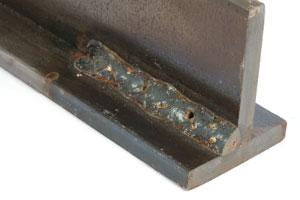
Advanced Solutions for Porosity Control
Executing cutting-edge technologies and innovative techniques plays a pivotal function in attaining premium control over porosity in welding processes. One advanced service is using innovative gas combinations. Shielding gases like helium or a combination of argon and hydrogen can aid lower porosity by providing better arc security and improved gas insurance coverage. Furthermore, using sophisticated welding methods such as pulsed MIG welding or changed ambience welding can likewise aid alleviate porosity problems.
One more innovative remedy entails making use of advanced welding devices. For instance, utilizing tools with integrated features like waveform control and advanced source of power can boost weld top quality and reduce porosity threats. The execution of automated welding systems with specific control over parameters anonymous can considerably minimize porosity defects.
In addition, including sophisticated tracking and examination innovations such as real-time X-ray imaging or automated ultrasonic testing can help in spotting porosity early in the welding procedure, permitting prompt restorative activities. On the whole, incorporating these advanced solutions can greatly enhance porosity control and boost the general top quality of bonded components.
Verdict
In final thought, understanding the science behind porosity in welding is vital for welders and makers to create top quality welds - What is Porosity. Advanced remedies for porosity control can further boost the welding process and make certain a strong and dependable weld.